Custom CNC Machining Manufacturer: The Future of Precision Engineering
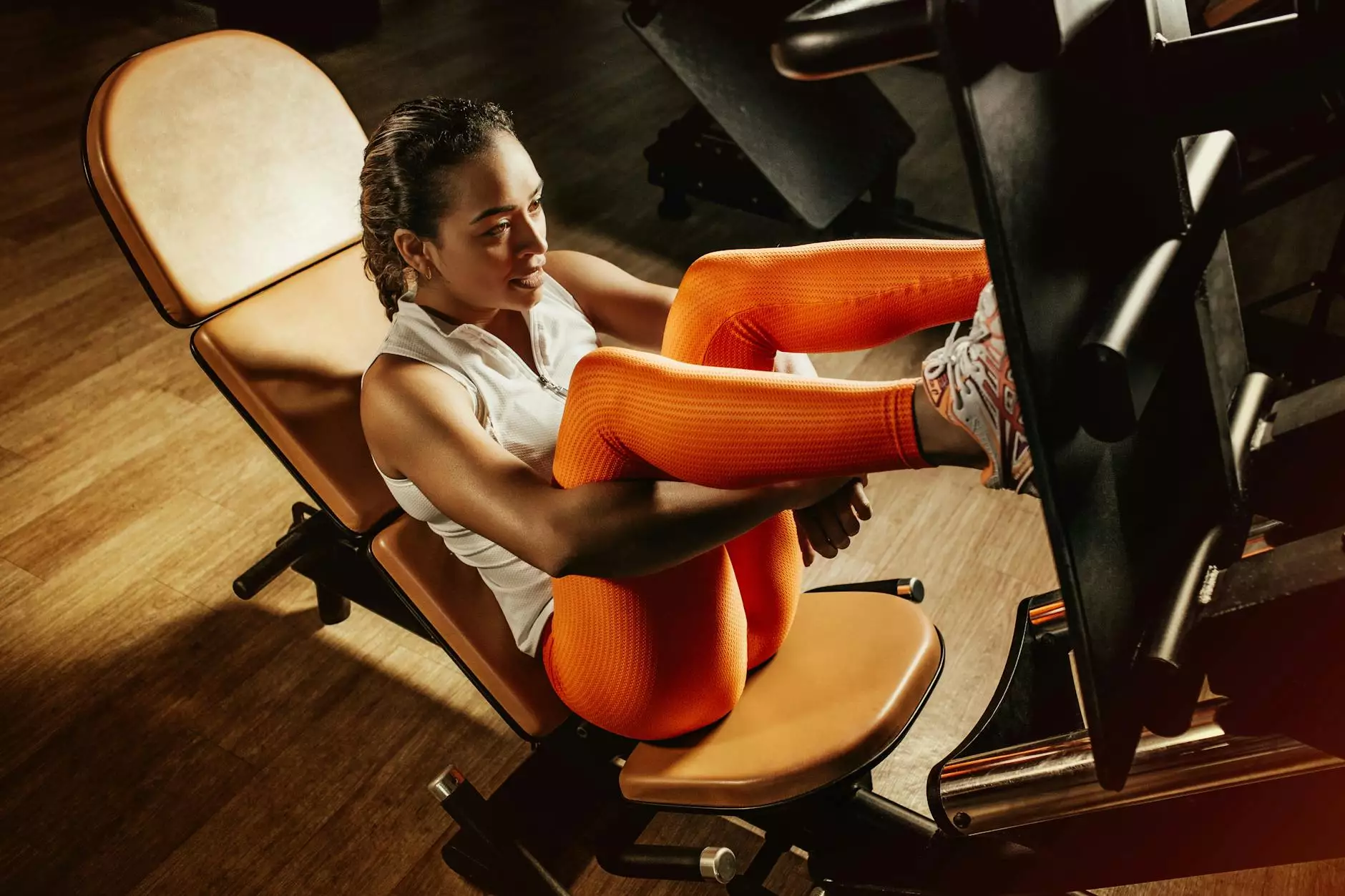
Introduction to Custom CNC Machining
CNC (Computer Numerical Control) machining is an advanced manufacturing technology that allows for the precise fabrication of parts and components in various industries. As a custom CNC machining manufacturer, DEEPMOULD stands at the forefront of this dynamic field, providing tailored machining solutions that meet the unique needs of our clients.
Understanding CNC Machining
CNC machining represents a transformative approach in the manufacturing sector, employing computer software to control machine tools like mills, lathes, and grinders. This technology offers unparalleled accuracy and repeatability, enabling manufacturers to produce complex geometries with ease. Here are some critical components of CNC machining:
- Computer Control: The heart of CNC machining lies in its computer control systems that direct the machining operations based on programmed specifications.
- Tooling: High-quality tools allow for the precise cutting of various materials, ensuring that the end product meets stringent quality standards.
- Materials: CNC machining can work with various materials, including metals, plastics, and composites, making it versatile for different applications.
The Advantages of Custom CNC Machining
Choosing a custom CNC machining manufacturer like DEEPMOULD offers several significant advantages for businesses looking to enhance their operations:
- Precision and Consistency: CNC machining delivers high precision, allowing for parts that fit and function perfectly, reducing the likelihood of errors.
- Efficiency: Automated operations minimize downtime and production lead times, enabling faster turnaround for custom projects.
- Flexibility: CNC machining is capable of producing both small batch runs and large-scale production, accommodating the evolving needs of manufacturers.
- Cost-Effective: Although the initial setup costs can be higher, the long-term savings in labor and material efficiencies lead to lower overall production costs.
Applications of Custom CNC Machining
The versatility of CNC machining makes it suitable for a myriad of applications across diverse industries. Here are some primary sectors where custom CNC machining is employed:
- Aerospace: Producing lightweight yet durable components for aircraft that meet stringent safety and performance standards.
- Automotive: Manufacturing high-precision parts, such as engine components and custom fittings, to enhance vehicle performance.
- Medical Devices: Creating intricate parts for surgical instruments and implants that require impeccable accuracy.
- Consumer Electronics: Designing and manufacturing components for devices that demand high precision and reliability.
The CNC Machining Process: Step by Step
Understanding the CNC machining process is crucial for appreciating its benefits. Here’s a step-by-step guide on how a typical custom CNC machining operation unfolds:
1. Design and Prototyping
The process begins with the creation of a digital design using CAD (Computer-Aided Design) software. This design is then converted into a CNC program using CAM (Computer-Aided Manufacturing) software. The program includes all instructions for the CNC machine.
2. Material Selection
Choosing the right material is critical. Depending on the application's requirements, a variety of metals like aluminum, steel, titanium, and plastics can be selected to achieve the desired performance characteristics.
3. Machining Process
The CNC machine executes the programmed instructions accurately, cutting the material into the required shape. Various techniques like milling, turning, and drilling can be employed during this stage depending on the complexity of the part.
4. Quality Check
Once machining is complete, rigorous quality checks are performed to ensure the parts meet specifications. Measurements are taken using precision instruments to verify all dimensions.
5. Finishing
The final step includes any additional finishing processes, such as coating, polishing, or anodizing, to enhance the appearance and durability of the components.
Choosing the Right Custom CNC Machining Manufacturer
When selecting a custom CNC machining manufacturer, it is essential to consider several factors to ensure you receive the best service. Here’s a checklist to help guide your decision:
- Industry Experience: Look for manufacturers with a proven track record in your specific industry.
- Capabilities: Ensure the manufacturer has the equipment and technology needed to produce the components accurately.
- Quality Assurance: Verify that the manufacturer employs stringent quality control measures throughout the machining process.
- Customer Support: A responsive customer service team is crucial for addressing any queries or issues that arise during production.
- Pricing: While cost is an important factor, it should not be the only consideration. Assess value against the quality offered.
The Future of CNC Machining
As technology continues to evolve, so will CNC machining. Innovations in artificial intelligence, machine learning, and automation are set to drive enhancements in precision and efficiency. Several trends are emerging in the industry:
- Integration of IoT: IoT technologies will enable real-time monitoring and analysis of CNC machines to optimize performance.
- Advanced Materials: Research into new materials will expand the application of CNC machining in various fields.
- Increased Customization: As businesses strive for differentiation, custom CNC machining will enable bespoke solutions that meet unique customer demands.
Conclusion
In today's competitive manufacturing landscape, partnering with a reputable custom CNC machining manufacturer like DEEPMOULD can provide businesses a distinct advantage. By leveraging the precision, efficiency, and versatility of CNC technology, companies can meet their production goals and innovate within their sectors. As we look to the future, embracing the advancements and trends in CNC machining will remain pivotal in fostering growth and success.