The Rise of Liquid Silicone Injection Molding Machines in Manufacturing
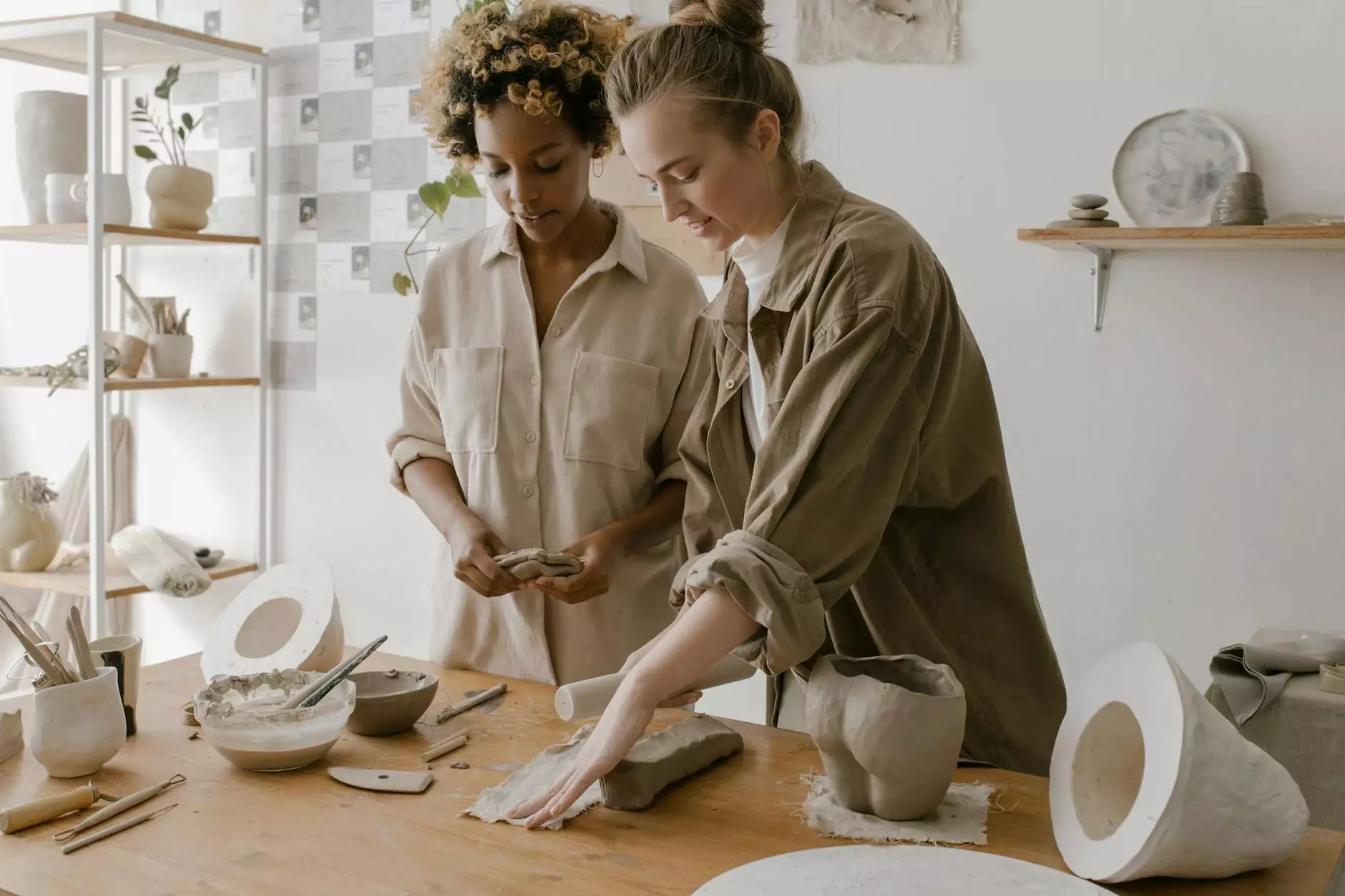
In the ever-evolving world of manufacturing, liquid silicone injection molding machines have emerged as a game changer, especially in the fields of electronics and medical supplies. These advanced machines not only enhance the production process but also improve the quality of end products. This article delves deep into the advantages, applications, and innovations associated with these machines while focusing on how companies like Nolato are setting benchmarks in the industry.
What is Liquid Silicone Injection Molding?
At its core, liquid silicone injection molding is a manufacturing process that involves the injection of liquid silicone rubber (LSR) into a mold to create detailed components. This technique offers immense flexibility and precision, making it ideal for high-performance applications in various sectors.
Key Features of Liquid Silicone Injection Molding
- High Temperature Resistance: LSR can withstand extreme temperatures, making it suitable for diverse environments.
- Biocompatibility: Many LSR formulations are biocompatible, vital for medical applications.
- Durability: LSR products exhibit excellent durability and can endure harsh conditions without degrading.
- Flexibility: Liquid silicone rubber remains flexible, allowing for complex shapes and designs.
The Importance of Liquid Silicone Injection Molding Machines
Why Choose Liquid Silicone?
Liquid silicone has become a top choice in manufacturing for numerous reasons:
- Efficiency in Production: The high-speed nature of liquid silicone injection molding allows for quick turnaround times.
- Cost-Effectiveness: Although the initial investment can be high, the efficiency gains lead to lower per-unit costs.
- Environmental Benefits: LSR is environmentally friendly, as it can often be recycled or reused, reducing waste.
Applications of Liquid Silicone Injection Molding Machines
The versatility of liquid silicone injection molding machines allows them to be used across various industries:
1. Electronics Industry
In the electronics field, manufacturers require materials that offer both protection and conductivity. Liquid silicone exhibits excellent insulative properties, making it suitable for:
- Seals and Gaskets
- Keypads and Switches
- Overmolding of Electronic Components
2. Medical Supplies
Healthcare products demand the highest standards of hygiene and reliability. Liquid silicone molding provides these through:
- Surgical Instruments
- Medical Implants
- Catheters and Tubing
Advantages of Investing in Liquid Silicone Injection Molding Machines
Quality and Consistency
One of the primary benefits is the quality and consistency of the products being manufactured. The precise nature of liquid silicone molding allows for tight tolerances and high-quality finishes, ensuring that every piece produced meets rigorous standards.
Innovations in Technology
Modern liquid silicone injection molding machines are equipped with advanced technology that further enhances production capabilities. Features such as:
- Automatic Mold Release Systems: These systems reduce downtime and optimize efficiency.
- Precision Temperature Control: Ensures that the silicon cures correctly for strong end products.
- Smart Manufacturing Software: Integration with IoT makes monitoring and optimizing production processes more accessible.
Challenges and Solutions in Liquid Silicone Injection Molding
Despite its advantages, this technology faces challenges, including:
Poor Adhesion to Other Materials
Liquid silicone has issues adhering to various substrates, which can be crucial in multi-material applications. Solutions involve using bonding agents or selecting suitable base materials that enhance adhesion.
Initial Investment Costs
The upfront cost of procuring liquid silicone injection molding machines can be significant. However, the long-term savings in efficiency and waste reduction often justify this initial expense.
Case Studies: Nolato's Leadership in the Industry
Nolato, a global leader in advanced polymer solutions, has effectively utilized the capabilities of liquid silicone injection molding. Their commitment to innovation can be observed in several projects, such as:
1. Medical Device Manufacturing
Nolato has developed various medical devices that require precision and reliability. Utilizing liquid silicone injection molding has enabled them to create devices that not only meet regulatory standards but also exceed customer expectations.
2. Consumer Electronics
In the electronics sector, Nolato has been at the forefront of designing protective covers and seals using liquid silicone. The durability and flexibility of the materials they use lead to superior product performance in the field.
Future Trends in Liquid Silicone Injection Molding
As technology continues to evolve, so does the potential for liquid silicone injection molding. Future trends to watch include:
Sustainability Focus
The demand for sustainable materials is growing. Manufacturers are looking for ways to reduce their environmental footprint, making recycled liquid silicone a valuable commodity.
Integration with Smart Manufacturing
Advancements in AI and machine learning are set to optimize the production process further, leading to greater efficiency, lower costs, and better product quality.
Conclusion
In conclusion, liquid silicone injection molding machines represent a significant step forward in manufacturing technology. Their versatility, efficiency, and quality make them indispensable in industries such as electronics and medical supplies. Companies like Nolato are leading the charge by innovating and optimizing their processes to provide high-quality solutions for their clients. As we look to the future, it is clear that the role of these machines will only expand, making them a crucial asset in modern manufacturing.
Investing in liquid silicone technology is not just about keeping up with the competition; it's about setting new standards in quality and innovation. As the industry evolves, staying ahead of these trends will be key to success.