Understanding the Oil Pump in Diesel Engines: The Heart of Performance
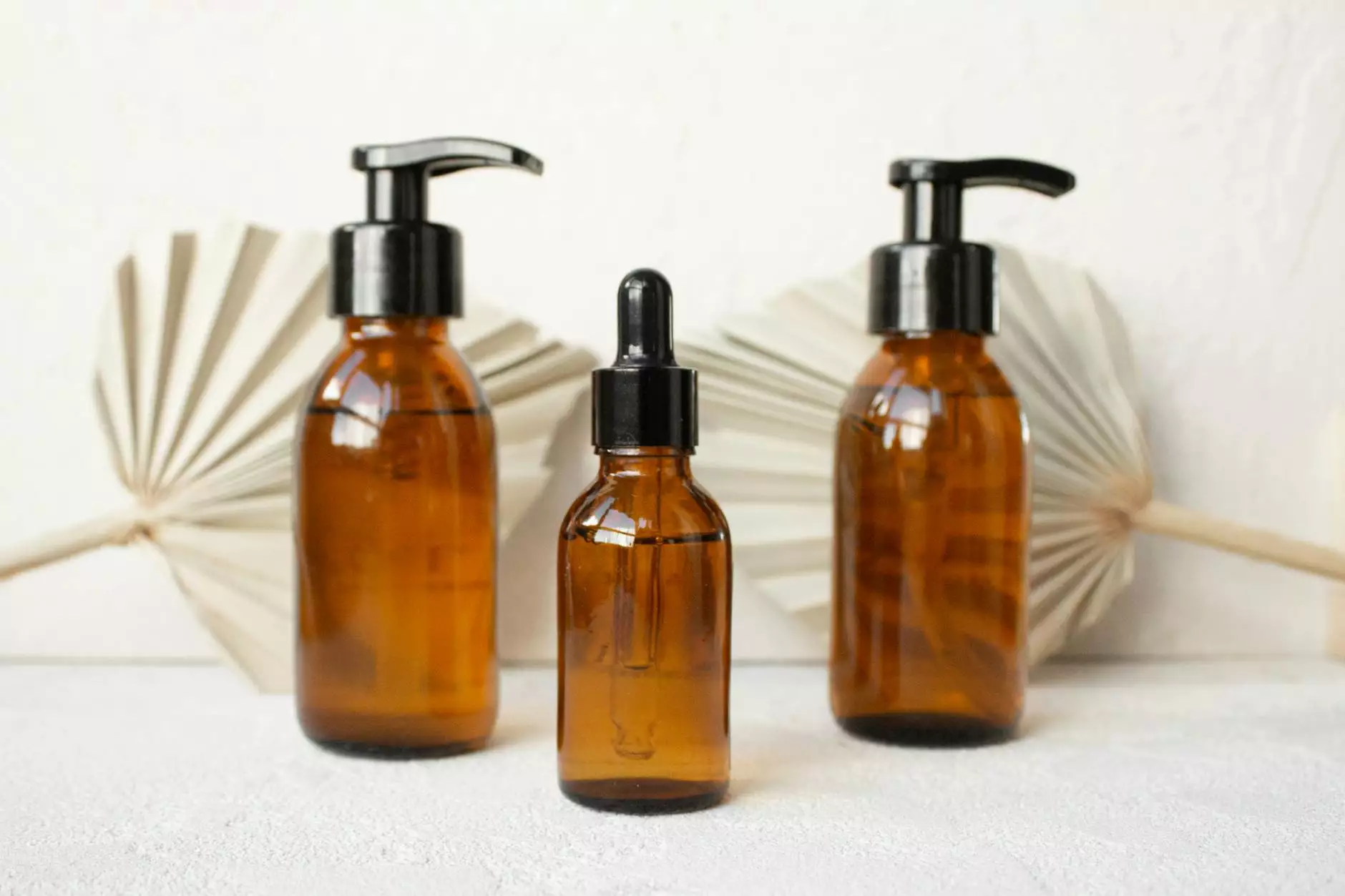
Introduction to Diesel Engines
Diesel engines are a cornerstone of modern machinery, powers vehicles, and drives industry. Their design intricately balances performance and efficiency, making them the choice for heavy-duty applications. Central to this performance is the oil pump in diesel engines, which ensures that all moving parts operate smoothly and efficiently.
The Role of the Oil Pump in Diesel Engines
The oil pump in diesel engines serves a critical role in librication and cooling. It pumps engine oil to various vital components, reducing friction and preventing excessive wear. Here are some key functions of the oil pump:
- Lubrication: Ensures all moving parts are properly lubricated, minimizing wear and tear.
- Cooling: Helps dissipate heat away from the engine components, maintaining optimal operating temperatures.
- Cleaning: Filters out contaminants and debris, which helps maintain the engine’s health.
- Sealing: Creates a seal that prevents oil leaks and enhances overall engine efficiency.
Types of Oil Pumps Used in Diesel Engines
Understanding the types of oil pumps available is important for both maintenance and replacement. Here are the most commonly used oil pump types in diesel engines:
1. Gear Pumps
Gear pumps are the most widely used in diesel engines due to their durability and efficiency. Their design consists of two gears that rotate to create a suction effect, drawing oil into the pump and pushing it through the engine. They are known for:
- High pressure output.
- Simple construction and reliability.
- Cost-effectiveness, making them a favorite among manufacturers.
2. Crescent Pumps
Crescent pumps are a type of gear pump with a crescent-shaped insert. They provide excellent flow characteristics and are particularly suited for applications requiring variable oil levels. Advantages include:
- Ability to handle thick oils due to their design.
- Good efficiency over a range of operating speeds.
- They’re adaptable for varying system demands.
3. Vane Pumps
Vane pumps use a series of vanes mounted to a rotor. As the rotor spins, the vanes extend and retract, allowing for the movement of oil. Key strengths include:
- Smooth flow output which reduces pulsation.
- Versatility for high output applications.
- Good performance at low speeds, beneficial for idle operations.
4. Rotary Pumps
Rotary pumps provide high efficiency and are often used in performance engines. Their ability to maintain consistent oil flow at higher speeds makes them ideal for many diesel applications. Benefits of rotary pumps include:
- Maintenance of pressure under various load conditions.
- Compact design suitable for tight engine layouts.
- Reliability and longevity across expansive work environments.
Importance of Regular Maintenance of the Oil Pump
Regular maintenance of the oil pump in a diesel engine cannot be overstated. A malfunctioning oil pump can lead to catastrophic engine failure. Here are some essential maintenance tips:
1. Check Oil Levels Regularly
Ensure that your engine oil levels are sufficient. Insufficient oil can result in inadequate lubrication and potentially severe damage.
2. Replace Oil Filters
Oil filters should be replaced regularly to minimize contamination of the oil. A clean filter ensures that the oil stays free of debris and maintains its lubricating properties.
3. Monitor Engine Temperatures
High engine temperatures can indicate problems with the oil pump or cooling system. Regularly monitoring these factors can help catch issues early.
4. Listen for Unusual Noises
Any unusual noises from the engine may indicate oil pump issues. Be proactive and investigate abnormal sounds immediately.
5. Consult Professionals for Servicing
Always seek professional services for significant engine work, especially when involving the oil pump. Expert technicians can accurately diagnose and fix issues before they lead to failure.
Common Issues with Oil Pumps in Diesel Engines
Several common issues can affect the functionality of the oil pump in diesel engines. Identifying these problems early can save time and money:
- Oil Leaks: Can lead to low oil levels and ineffective lubrication.
- Low Oil Pressure: Often caused by worn pump gears or blocked passages.
- Noisy Operation: Unusual sounds could indicate mechanical failure or inadequate lubrication.
- Overheating: Can result from insufficient oil circulation or pump failure.
- Contaminated Oil: Poor oil quality can lead to pump damage and degradation of engine components.
The Relationship Between the Oil Pump and Engine Efficiency
The efficiency of a diesel engine is closely tied to its oil pump performance. A well-functioning oil pump guarantees proper lubrication, leading to:
1. Enhanced Performance
With the right oil pressure and flow, all engine components can operate at peak efficiency, leading to improved performance.
2. Increased Longevity
Regular maintenance and functioning oil pumps reduce wear, thereby prolonging the lifespan of the engine.
3. Better Fuel Economy
Efficient lubrication translates to less internal resistance. This can lead to improved fuel economy, which is a critical concern for businesses relying on diesel engines.
4. Reduced Emissions
Efficient engine performance helps in reducing the amount of unburned fuel escaping into the environment, leading to lower emissions.
Conclusion: The Oil Pump as a Critical Component
In the world of diesel engines, the oil pump is vital to ensuring operational efficiency, longevity, and performance. By understanding its function, types, and maintenance requirements, operators can achieve optimal engine performance and reliability.
Partnering with quality spare parts suppliers like client-diesel.com will ensure that you have access to the best in diesel engine parts, including high-quality oil pumps designed for durability and efficiency. Regular checks and timely replacements can safeguard your investment in diesel technology, leading to consistent performance and operational success.
© 2023 Client Diesel. All rights reserved.