Exploring Tool and Die Casting: A Vital Process in Metal Fabrication
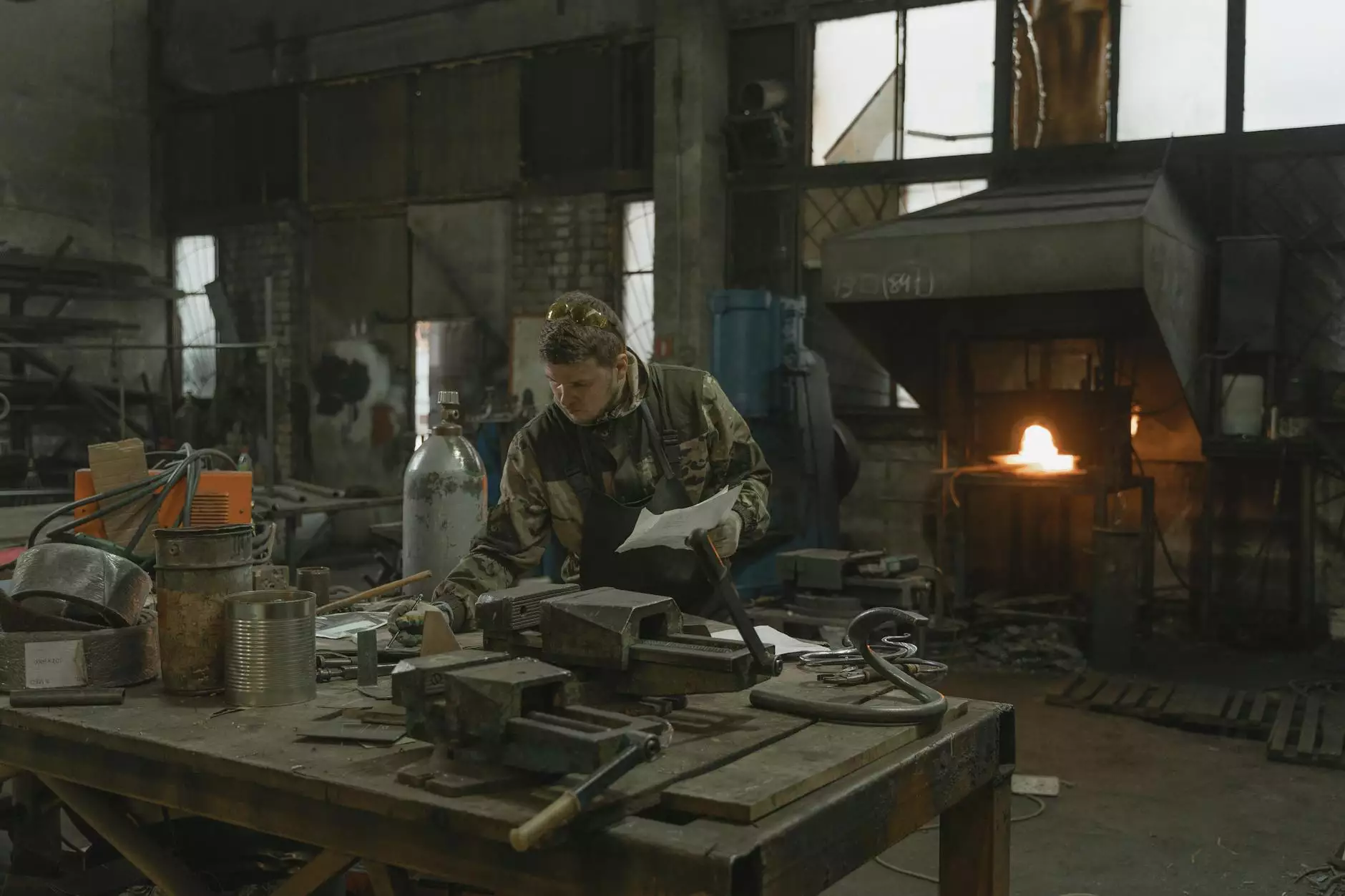
Tool and die casting is an essential technique in the realm of metal fabrication, significantly impacting various industries and applications. This article delves into the intricacies of tool and die casting, elucidating its processes, benefits, real-world applications, and why businesses like Deep Mould stand out in this field.
What is Tool and Die Casting?
Tool and die casting is a manufacturing process that involves the creation of tools and dies used for shaping materials, primarily metals, into desired forms. This method is pivotal for producing intricate parts and components that require high precision and repeatability.
The Process of Tool and Die Casting
The process of tool and die casting encompasses several key stages:
- Design and Engineering: The initial step involves the design of the tools and dies utilizing sophisticated CAD software. This stage is crucial for creating accurate specifications that align with the product requirements.
- Material Selection: Choosing the right materials for tool creation is vital. High-quality steel alloys are typically utilized for tools because of their durability and resistance to wear.
- Machining: Once the materials are selected, the tools and dies are machined. This involves cutting, shaping, and finishing the metals to meet precise dimensions and tolerances.
- Testing: The newly created dies are subjected to rigorous testing to ensure they perform as expected under production conditions.
- Production: After successful testing, the production phase begins. Molten metal is poured into the dies to create the final products.
- Finishing: The last step includes processes like cleaning, polishing, and additional machining to ensure the final product meets quality standards.
Benefits of Tool and Die Casting
There are numerous advantages to utilizing tool and die casting in manufacturing:
- Precision: One of the standout benefits is the level of precision that can be achieved. Products manufactured via this method typically have tight tolerances, which is critical for many applications.
- Cost Efficiency: Although the initial set-up costs can be high, mass production through die casting often leads to significant savings over time due to reduced material waste and faster production speeds.
- Versatility: Tool and die casting can accommodate various shapes and sizes, making it an adaptable solution for many industries.
- Durability: The components produced are known for their strength and durability, capable of withstanding harsh operating conditions.
- Reduced Lead Times: With modern manufacturing techniques, the lead times from design to production can be drastically shortened, enabling quicker delivery to clients.
Applications of Tool and Die Casting
The applications for tool and die casting are vast and varied. Some of the most significant sectors include:
- Aerospace: Components used in aircraft require high precision and reliability, making die casting a suitable process.
- Automotive: The automotive industry extensively uses die casting for producing engine blocks, transmission cases, and other critical parts.
- Consumer Electronics: Products such as smartphones and laptops utilize components made through this method for their intricate designs.
- Medical Devices: In the medical field, components that address patient safety and functionality benefit from the precision of die casting.
- Construction: Heavy machinery and construction tools often feature die-cast metal components that ensure robustness and reliability.
Deep Mould: A Leader in Tool and Die Casting
Deep Mould has earned a reputation as a premier provider of tool and die casting services. With a commitment to quality, innovation, and customer satisfaction, Deep Mould integrates the latest technologies in its manufacturing processes.
Why Choose Deep Mould?
When it comes to sourcing your tool and die casting needs, several reasons make Deep Mould the optimal choice:
- Expertise: With years of experience in the industry, Deep Mould possesses the know-how to tackle even the most challenging projects.
- Cutting-Edge Technology: The company continually invests in advanced technology to ensure high-quality production capabilities.
- Customized Solutions: Deep Mould prides itself on providing tailored services to meet the specific needs of its clients.
- Quality Assurance: Every product undergoes rigorous quality control processes to ensure it meets the highest standards.
- Excellent Customer Support: The company is dedicated to providing exceptional customer service, assisting clients throughout the entire manufacturing process.
The Future of Tool and Die Casting
As technology continues to advance, the future of tool and die casting appears promising. Innovations such as 3D printing and advanced simulation software are poised to transform how products are designed and produced.
Emerging Trends
Several trends are shaping the future landscape of tool and die casting:
- Increased Automation: Automation technologies are driving efficiency and precision, reducing labor costs, and improving production times.
- Sustainability Initiatives: Many manufacturers are exploring eco-friendly materials and processes to minimize environmental impact.
- Smart Manufacturing: The incorporation of IoT and data analytics in die casting operations offers real-time insights into production efficiencies and quality control.
- Adoption of Advanced Alloys: The development of new metal alloys is enhancing the performance characteristics of die-cast components.
Conclusion
In conclusion, tool and die casting plays a pivotal role in the metal fabrication industry, offering various benefits and applications across multiple sectors. Businesses seeking precision, durability, and cost-effective manufacturing solutions can trust Deep Mould to deliver high-quality products tailored to their needs. As the industry evolves with new technologies and sustainable practices, companies like Deep Mould are well-positioned to lead the charge into a brighter future.